A smart robotic way to go through your printed photos automatically.
Thanks to a smartphone you can go through your photos instantly, everywhere and every time. Unfortunately, this makes us lose that unique feeling: print memories and make them last forever. Somebody could confute that this is just a way to store useless and bulky stuff, but I found the way to give a "new life" to tons of photos forgotten in the basement.
I uploaded all versions of my project because I would like to explain you the entire process from the idea itself.
NOTE: none of this version is yet optimized for 3D printing (or any crating process), I will do that after we solve problems that we are able to see in the 3D model. Every version has a list of problems that I noticed, but the last option is always "..." to encourage you to find more, thank you for your collaboration: write me if you think you can help me or even just to ask questions about it. I will appreciate it.
V1
I thought that using two different frames was easier, so I decided that the frame had to be equipped with a small robot arm (with 9g servo motors) and a suction cup. The arm is long enough to reach the middle line of the picture box, take one photo with the suction cup (and a small 9g motor with a syringe to create vacuum) and position the photo in the other side of the frame. In this way all the photos are shown and (theoretically) it should work.
Problems:
- ∘ very big;
- ∘ the photos in the middle of the column are shown more frequently than the ones at the beginning and at the end;
- ∘ too many motors [6] (many things can go wrong, I would like to keep is simple, and it would be too noisy);
- ∘ ...
V2
The idea was to create something able to take the first photo and place it under the column of photos. In this way each photo will be shown just once every cycle, solving the 1st problem of the previous version. I thought about using a long linear actuator with a rubber piece at the end that could drag the first photo down the pile. A small ramp (in the frame) could leave the space for the entrance of the photo under the pile and the arm could push the photo. In this way only 3 motor were used, solving the 3rd problem.
Problems:
- ∘ very big;
- ∘ how should the design be completed?;
- ∘ will it work in a nearly vertical position?;
- ∘ ...
V3
3rd and 4th problems pushed me to think about a new version, without wasting more time. I thought about adding a moving-bridge style actuator, to take the photo from the top of the pile (with vacuum gripper) and put it where the linear actuated arm (as in V2) will be able to push it under the pile.
Problems:
- ∘ very big;
- ∘ too many motors [6] (many things can go wrong, I would like to keep is simple, and it would be too noisy);
- ∘ ...
V4
The V3 pushed me to think again about the V1, a moving-bridge stile actuator could solve the 3rd problem (the worst). So I decided to give it a possibility.
Problems:
- ∘ very big;
- ∘ the photos in the middle of the column are shown more frequently than the ones at the beginning and at the end;
- ∘ ...
V5
I think that using 2 mm plexiglass as the main material may "solve" the 1st problem of all designs: transparent material might make the project look smaller than it really is. As suggested from you, I've also added a "single sided bridge" instead of the big one of the previous design. I really like this idea, but I'm not sure about the strength of my design. Two boxed (probably made out of plastic, to hide cables and electronics) were added.
Problems:
- ∘ big;
- ∘ the photos in the middle of the column are shown more frequently than the ones at the beginning and at the end;
- ∘ strong enough?;
- ∘ ...
V6
The strength problem was solved: I added 3D printed linear bearings and 8mm metal rod to slide on. I also decided to change the motors: 28BYJ-48 stepper motor are still cheap, but more quiet and precise than 9g servo. I also added a 503012 hall effect sensor and a magnet, to have an absolute position of the actuators. I'm really satisfied by this design, but I still have to figure out how to add a suction cup: I think that the syringe method has too many weaknesses.
Problems:
- ∘ big;
- ∘ the photos in the middle of the column are shown more frequently than the ones at the beginning and at the end;
- ∘ how should the suction cup be?;
- ∘ ...
V7
All the electronics (microcontroller and motor drivers) are now hidden in the arm. In this way the main frame is just build from plexiglass pieces, removing the two boxes. This will make it look even smaller than before.
The suction cup is added at the end of the vertical sliding arm and connected, with a tube, to a mini electromagnetic solenoid valve. This will be open while the arm press the suction cup on the photo (to let air out) and closed while the photo needs to be carried to the other side. In this way no external air pump will be needed and, proved after some test, the suction will be strong enough to lift the photo and responsive enough to let the photo fall down when needed.
Problems:
- ∘ the photos in the middle of the column are shown more frequently than the ones at the beginning and at the end;
- ∘ ...
V8
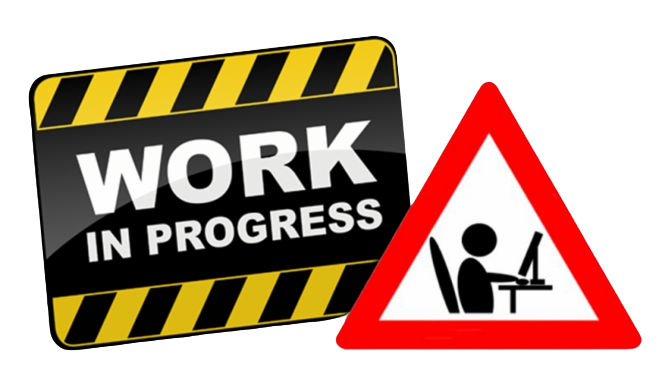
Some testing led to several key enhancements to the project.
The linear guides were replaced with proper 8mm linear bearings, resulting in smoother operation and eliminating unexpected movement and noise. Additionally, the design was optimized for laser cutting, utilizing 2mm plexiglass for the main frame and incorporating a 3D-printed divisor, promoting easier fabrication. Finally, the arm received an organic shape to enhance aesthetics, while the microcontroller was swapped for a more compact Arduino Pro Micro.
These improvements not only enhanced functionality and manufacturability, but also contributed to a more visually appealing design.
Problems:
- ∘ the photos in the middle of the column are shown more frequently than the ones at the beginning and at the end;
- ∘ ...